31 Mar 2021
Published in: Concrete Magazine, March 2021
As we try to lower our carbon footprint and produce lower carbon intensive projects, one of the ways we can do so is to look at how we specify the concrete we use. Jenny Burridge of The Concrete Centre.
Concrete is made from aggregate, cement and water; admixtures can be, and normally are, included in the mix. In terms of embodied carbon for the different constituents, aggregates and water have very low embodied carbon. Locally sourced primary aggregates have an embodied carbon of about 4kgCO2/tonne. It is the cement, forming about 10–15% of the mix, which holds most of the embodied carbon.
In October 2020, the UK Concrete and Cement industry launched its Roadmap to Beyond Net Zero(1). The roadmap shows how the industry can continue its decarbonisation journey, with the aim of providing net zero concrete by 2050. The industry has already taken considerable early action and due to investment in fuel switching, changes in product formulation and energy efficiency, including plant rationalisation, its direct and indirect emissions are 53% lower than 1990. The roadmap shows that the industry could become net negative by 2050, removing more carbon dioxide from the atmosphere than it emits each year.
Although a net zero concrete is not yet available, it is possible to save carbon now by specifying low-carbon concrete using cement replacements, or low carbon cements. All concretes to BS 8500(2) are based on Portland cement, or CEM I, but most contain secondary cementitious materials (SCMs) or additions, such as GGBS, fly ash, silica fume, limestone powder and pozzolana. These SCMs have a much lower embodied carbon than CEM I and can make significant savings to the embodied carbon of concrete (see Table 1).
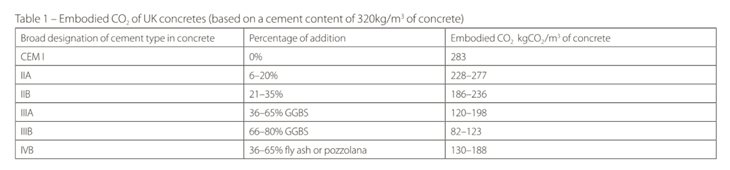
Since the latest version of BS 8500, ternary blends of cements have been allowed. These use CEM I with two types of additions, normally limestone fines with either fly ash or GGBS. All these cements are based on CEM I, but there are also geopolymers or alkali-activated cementitious materials (AACMs) that can be specified using PAS 8820(3), which is a publicly available specification produced by British Standards Institution. These are normally based on GGBS, activated by a chemical which is added to the mix.
One of the things to note with the use of low-carbon concrete is that the higher the proportion of additions, the slower the strength gain of the concrete. This might not influence the construction programme if the concrete does not need to be struck quickly or support load shortly after being cast. For example, foundations are frequently cast against the ground and the load is applied only slowly as the project progresses. Although the standard concrete strength is specified at 28 days, a concrete made with IIIB cement will still be gaining strength at that stage and the strength at 56 days may be 40% greater than that gained by 28 days. The designer could take advantage of this by specifying a 56-day strength.
Elements that need to have a faster strength gain, such as suspended slabs or post-tensioned elements, can still use additions and do not need to be restricted to using CEM I. There have been several projects that have used a CEM IIIB for a post-tensioned suspended slab and concrete producers can add a set accelerating admixture to the concrete to improve the setting time.
Designers should also be aware that in some instances the use of higher strengths of concrete, that require a larger proportion of cement, can also reduce the embodied carbon of a structure, as less concrete is required. The use of structurally efficient sections, such as rib or voided slabs, also reduces the volume of concrete and hence the embodied carbon. Superplasticiser admixtures can also help reduce the embodied carbon by reducing the water:cement ratio and hence providing a stronger concrete for the same quantity of cement.
If in doubt, the simplest way forward is to specify performance and use designated concretes. This will increase the opportunity for the concrete supplier to provide a low-carbon concrete. There is also a range of proprietary low-carbon concretes available and early engagement with the concrete supplier enables the company to provide advice on what can be achieved for the location and needs of the project.
In summary, the embodied carbon of concrete can be lowered by:
- specifying low-carbon concrete and cements that use secondary cementitious materials
- if your project has the right conditions, AACMs and geopolymers maybe an alternative and can be specified using PAS 8820
- specifying 56-day or 90-day strengths where appropriate to enable lower-carbon concrete to be used
- considering the embodied carbon of the whole structure and whether the volume of concrete can be reduced, for example by using high-strength concrete or ribbed or voided slabs.
- specifying performance, using designated and proprietary concretes and engaging with your concrete supplier to understand the low-carbon concrete options available.
References
- MPA–UK CONCRETE. UK Concrete and Cement Industry Roadmap to Beyond Net Zero. MPA–UK Concrete, London, 2020.
- BRITISH STANDARDS INSTITUTION, BS 8500. Concrete – Complementary British Standard to BS EN 206. Part 1 – Method of specifying and guidance for the specifier. BSI, London, 2015 +A2:2019.
- BRITISH STANDARDS INSTITUTION, PAS 8820. Construction materials. Alkali-activated cementitious material and concrete. Specification. BSI, London, 2016.
Further reading: Specifying Sustainable Concrete
Written by - Jenny Burridge Head of structural engineering, The Concrete Centre