3D printed concrete
“We had a crazy idea, and no idea how it could be made to work”
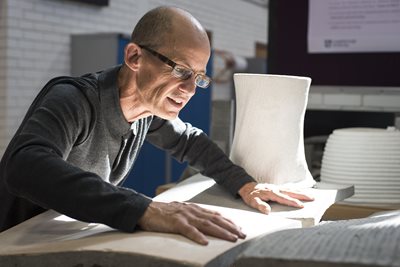
In 2006 a project co-led by Loughborough University’s Professor Simon Austin became one of the first in the world to research the possibility that concrete could be 3D printed. “We were starting absolutely from scratch,” he recalls. “We had a million pound grant, a crazy idea, and no idea how – or even if – it could be made to work.”
Some 18 months later, the team had created a 5m-tall gantry with a system of chains and drives via which a concrete delivery nozzle could be moved in three dimensions. “It was quite a thing,” he says. “When sixth-formers visited on open day, they naturally tended to gather round it and wanted to know what it did.” This, says Austin, is one of the most remarkable things about the 3D printing of concrete: “It captures the imagination. I had grown accustomed to eyes glazing over when I told people I researched concrete. But 3D-printed concrete is different. People are immediately excited by its potential. Suddenly concrete is sexy.”
It is certainly fascinating to watch, as the beads are laid down and the elements take shape, but getting it to work is far from simple. “You have to get the rheology exactly right,” says Austin. “You’re looking for the Goldilocks ideal: too thick and it won’t flow; too runny and it won’t stand up.” This is tricky for, as Austin puts it, “concrete is one of the most complex chemical products on the planet. Even cement chemists don’t fully understand it.”
Their initial Engineering and Physical Sciences Research Council (EPSRC) project completed in 2011. By then, the idea of printing buildings had begun to attract considerable attention. Videos of houses being crudely printed in China went viral on YouTube, while Loughborough’s own, featuring Austin and his colleague Professor Richard Buswell, has attracted more than 600,000 views.
Loughborough’s technology has continued to progress, with the help of further EPSRC and TSB government funding and contributions from partners including Foster + Partners, Skanska, ABB, Tarmac and Hyundai. “The gantry has been replaced by a more accurate robotic arm, and concrete can now be laid down at a rate of 50cm a second.
We can produce elements that curve in three planes, and that contain overhangs and voids. And although there are now more than 30 concrete printing projects globally, we remain in the forefront of world research.” Loughborough scientists have also created a start-up Concrenetics, which is partnering with Belgian precast company Urbastyle, with a view to providing commercially viable products.
Regulatory issues alone will mean that it may still be five to ten years before 3D printing becomes a commonplace solution for bespoke concrete elements. But one day it will be routine. Of that, Austin, the man who was in it from the start, has no doubt.
Words by Tony Whitehead
Photo Paul Burroughs
Published in CQ Autumn 2019