BioZeroc
A Cambridge start-up is using bacteria to create cement-free concrete. Now they just have to prove that these tiny microbes can work at scale…
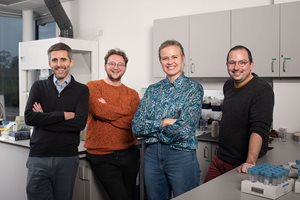
The drive to decarbonise concrete is progressing on several fronts, each with exciting potential. One of the most intriguing areas of research focuses on replacing cement with bacteria. Unlikely as it sounds, some microorganisms can bind the aggregate used in concrete by precipitating calcite, the naturally occurring form of calcium carbonate. BioZeroc, a Cambridge-based start- up, is using this capacity to create cement-free concrete.
Co-founder Liv Andersson, a former sustainability professional with qualifications in architecture, engineering and ecology, explains: “In my old job, I worked to reduce the carbon embodied in new buildings and, sure, good design can significantly reduce a carbon footprint. But for me, in the end, it was not enough. We need new approaches – new materials – if we are to go further and get to a zero-carbon construction industry.”
Andersson became fascinated by the use of calcite- precipitating bacteria to stabilise soils, and in self-healing concrete (see CQ 270, winter 2019). “I thought, suppose you could scale up this process to create larger, more solid material? Suppose you could make concrete this way? If you use microbes rather than cement to bind aggregate, that alone cuts concrete’s carbon footprint by about 85%.”
Andersson met scientist John Somerville through Carbon13, a Cambridge-based organisation that brings together entrepreneurs and scientists. For the past year, together with experimental biologist Davor Ivankovic and microbiologist Laurence de Lussy Kubisa, they have been exploring how to encourage their microbes to work at scale: “Our unofficial motto is from the Daft Punk track: harder, better, faster, stronger!” says Andersson.
“The speed of calcite production depends on many things, including the food you give the bacteria, and the conditions in which they thrive. Our process control has succeeded in greatly accelerating calcite production. This is where the gold in our technology lies.” The latest samples (see below) are about four times thicker than the previous batch.
Andersson can say little about how they have achieved what she calls “the magic”. This is still very new and patents are pending. But on her desk are two small pieces of concrete: “This one is made with cement,” she says, “while this one has the same aggregate, but no cement at all. I can’t say exactly how we do it, but the ingredients are inexpensive and widely available. And, if we succeed in sourcing feedstock chemicals from waste sources, the resulting concrete could be carbon-negative.”
The BioZeroc concrete is whiter than its cement-based equivalent and has a fine texture. “It is in some ways like marble – smoother and less porous than standard concrete – but these are properties that we should be able to
control as we refine our processes.” Facade panels are one potential application, as are bricks – as smaller, repeatable elements, they enable faster iteration.
BioZeroc expects to create its first full-size brick early in 2023 and to exhibit a larger structure later in the year. “There is an eagerness to use the product, but we have to be patient. Right now our concrete is made with a lot of love in a lab. We need to get it to the point where it can be reliably produced at scale in a factory. So, yes, if you like, harder, better, faster stronger!”
Interview by Tony Whitehead
Photos Paul Burroughs
Published in CQ Winter 2022