Carbon capture algae
“What excites me about this carbon reduction project is that we can do it now”
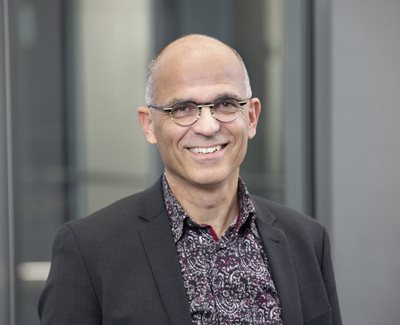
As group director of alternative resources for HeidelbergCement, Jan Theulen is involved with a wide range of projects designed to help the company achieve CO2 neutral status by 2050. HC – which operates as Hanson in the UK – has initiatives looking at carbon capture and low-carbon cement formulae, and other projects sourcing alternative fuels for its plants. But one of the most intriguing and, one senses, one of Theulen’s favourites, lies almost 100 miles north-west of Marrakesh – at Safi on the Atlantic coast.
Here, next to HC’s largest plant in Morocco, are row upon row of long plastic tubes filled with a carefully mixed cocktail of algae and brine. Waste CO2 from the cement plant is bubbled through the water and the algae thrive on it, absorbing up to twice their own weight in the gas as they grow and reproduce.
“The Safi site is ideal for this project,” explains Theulen. “The algae like the mild maritime climate, and the good hours of light and sunshine. And we like the availability of non-arable land and a skilled, reliable workforce.” Once the algae has absorbed its fill of CO2, it is pumped from the tubes and filtered from the brine.
“It is then dried in a solar dryer,” says Theulen, “similar to the ones used to dry dates and fruit in the region. It’s essentially a box with a fan to direct a flow of sun-heated air over the algae.” The result is dried algae flakes, rich in nutrients such as Omega 3 and 6 fatty acids: “These can be sold as fish food or chicken food to help offset the costs of the project.”
At present, the plastic tubes of the algae farm cover just one hectare, but Theulen wants to scale up to 400ha, when the algae will consume about 10% of the plant’s CO2 output. Modest beginnings do not worry him unduly. “In the past I have worked extensively setting up alternative fuel supplies derived from waste for our cement plants, also starting small. I know it takes time, you need to get local entrepreneurs involved, you need to build robust supply chains, you need to demonstrate a good business case to make it happen.
And so once we have created an efficient algae business, we can then hand it over to companies in that market. After all, we are not fish-food producers.” Theulen himself is a mechanical engineer who has been with HC for 30 years. He was originally on capital projects to design and set up new plants, but has focused on environmental initiatives for the last decade. “What excites me about this project is that we can do it now. As an engineer, I don’t like to just talk about things. I want to make them happen.”
Interviewed by Tony Whitehead
Photo HeidelbergCement
Published in CQ Summer 2020