Cutting carbon with Concept
The embodied carbon of concrete structural frames can vary widely. Emily Halliwell introduces a tool to guide designers to the most material-efficient solutions
Concept is a free spreadsheet-based design tool from The Concrete Centre. It enables users to compare a wide range of concrete frame options, ranking them in terms of carbon, cost or construction time.
As its name suggests, Concept is intended to be used early in the design process, when there is the greatest scope to reduce embodied carbon by amending design criteria, reconsidering space planning and exploring different construction methods.
At concept stage, it can be difficult to quantify the impact of changing grid spacing, loading or framing type, so the tool offers a simple way to compare different options. As Concept can quickly generate element sizes and comparison data, it may also be useful whenever there is an opportunity to consider alternative frame types, loads or spans.
Optimising structural design: the key principles
Optimising the amount of material in a concrete frame can make a significant difference to its embodied carbon. Concrete frames can be designed in many different ways, and there are many parameters to consider when improving material efficiency.
■ Grid spacing: Smaller grid spacing and corresponding shorter spans typically lead to reductions in the required structural depth, and therefore in material quantities. The aspect ratio of each bay also impacts efficiency. Square bays are typically more efficient for two-way spanning systems; for one-way systems, rectangular bays are usually more efficient.
■ Loading: Reduced loading also leads to reductions in structural depth. For this reason, excessive or blanket allowances for loading associated with finishes and services should be avoided. For building services and plant rooms, they should ideally be based on the weight of the equipment that will be installed, using data from the manufacturer. Live load allowances should be discussed with clients, particularly where project requirements exceed those of the Eurocodes.
■ Structural systems: The best framing solution for each case depends on a number of factors, including building use, load and span. Typically, deeper systems, such as ribbed
slabs or slabs on beams, are more materially efficient than shallow systems, such as flat slabs. Where long spans, high loads or irregular layouts are necessary, it is important to select the optimal solution. For example, beams can be used to support large point loads or to accommodate irregular grids. Flat slabs are more appropriate for regular column grids, and are not suitable for large point loads.
Structural systems that incorporate voids, such as ribbed and waffle slabs and precast hollowcore slabs, minimise the use of concrete where it is not required. Permanent void formers can also reduce the weight of the structure and the volume of material needed for the structure and foundations. However, the increased depth associated with some structural systems can have implications for overall building height and the distribution of services.
Post-tensioning should be considered wherever long spans are required, or structural depth is critical. This increases strength by adding pre-compression into concrete after it has been cast, which means slabs can be slimmer. Post-tensioning is often used in flat slabs, but is also applicable to ribbed and waffle slabs, enabling even greater embodied carbon reductions. Hollowcore planks typically use prestressing, along with cores or voids along their length, making them structurally and materially efficient.
What can we learn from Concept?
Designers may be reluctant to propose significant changes in loading to a client, or much shorter spans. But smaller changes can also add up to big carbon savings.
In our first example, we look at how a series of recommendations can lower the embodied carbon of a baseline scheme by 42%, before the concrete mix specification is even considered. Taking an office building with five bays in each direction, each spanning 9m, we assume a typical office floor load of 5kN/m2, made up of an imposed load of 4kN/m2 and an allowance of 1kN/m2 for partitions. A flat slab is selected, as flat soffits can simplify the installation of partitions and services.
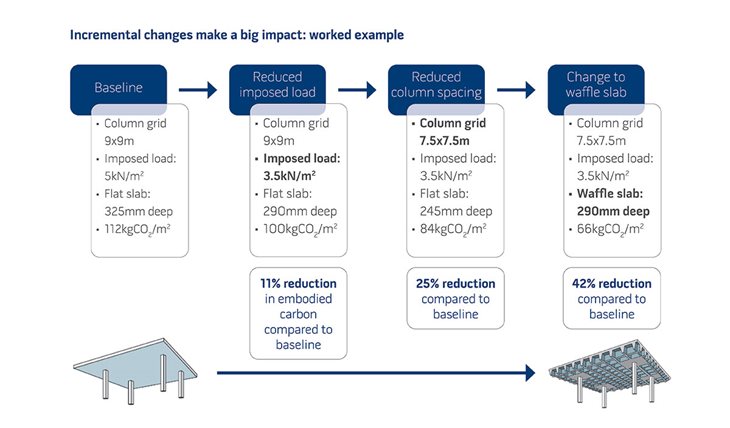
Step 1: Reduce the imposed load
The UK National Annex of Eurocode 1 recommends an imposed load for offices of 2.5kN/m2, with 1kN/m2 for partitions, reducing the imposed load from 5kN/m2 to 3.5kN/m2. This means that the slab depth may be reduced, with smaller columns, leading to an embodied carbon reduction of 11%.
Step 2: Reduce column spacing from 9m to 7.5m
This allows the 1.5m planning grid to be used and is one of the options in the British Council for Offices’ 2023 guidelines. The footprint of the building remains the same, but the number
of bays is increased from five to six. In combination with the reduced imposed load, this results in a 25% reduction in embodied carbon compared to the baseline scheme.
Step 3: Change the structural floor type to a waffle slab
The combined changes in column spacing and loading mean that the proposed waffle slab solution is 290mm deep, compared to 325mm for the flat slab in the baseline scheme, resulting in an embodied carbon reduction of 42%. This also offers more space for floor build-up and services, or opportunities to reduce the overall building height. The increase in surface area provided by the waffle slab enables greater potential use of thermal mass for heating and cooling.
Consider wide beams when depth is critical
More material-efficient floor systems such as ribbed or waffle slabs are typically deeper than flat slabs. This can be a challenge on schemes where floor depth is critical – if building heights are limited by planning restrictions, an increased floor build-up could come at the cost of an additional storey.
Post-tensioning (PT) is a common solution to this. Another that is often overlooked is wider beams, which offers material efficiency with reduced depth. In our second example, we switch from beams 300mm wide and 525mm deep, to beams 2,400mm wide and 300mm deep. This reduces overall floor depth by 225mm, with only a 3% rise in embodied carbon.
While further depth reductions are possible – for example, a 250mm-deep flat slab or a 200mm-deep PT flat slab – these significantly increase embodied carbon, by 23% and 15% respectively. Wide beams also reduce slab spans, allowing for a thinner slab and offsetting the additional material used in the beams.
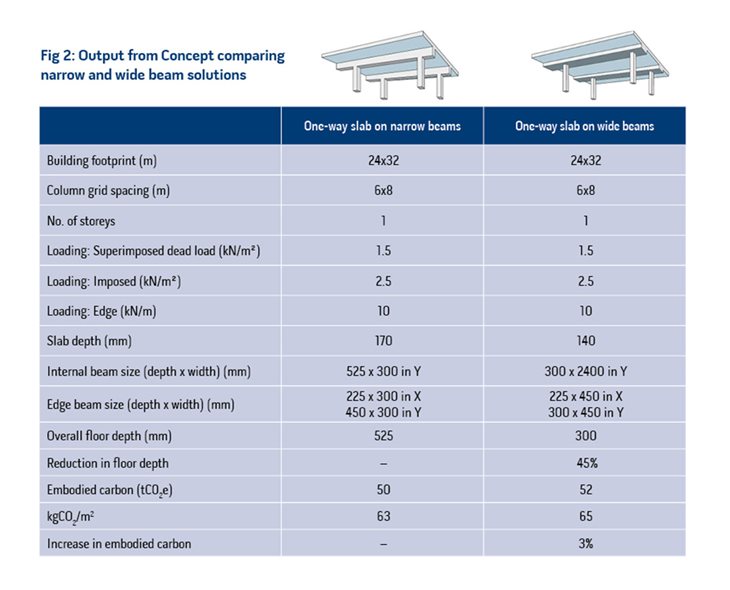
When longer spans are more efficient
Typically structural depths increase as spans rise, requiring greater quantities of material to span longer distances. However, this isn’t always the case for solutions involving hollowcore planks. These are generally proprietary systems and come in fixed unit depths, which will have a maximum span for the specified load. Designers should consider using spans close to the maximum to make the best use of the material.
In our third example, we take a building with an imposed load of 7.5kN/m2. When the hollowcore planks span 7m, supported by beams spanning 12m, the embodied carbon is 128.4kgCO e/m2. Increasing the span of the hollowcore planks to 8.5m, supported again by beams spanning 12m, reduces this to 125.7kgCO e/m2. This means a 21% increase in the span (and area of the bay) and a 2% reduction in embodied carbon. The supporting beams may be larger or need more reinforcement as the span of the hollowcore planks rises, but in this example the beam depths remain the same – 825mm. (Here, embodied carbon is compared per unit of area, because the footprint of the building changes with the span.)
Beyond the frame: what else do designers need to consider?
The Concept tool only considers life cycle stages A1-A3, also known as cradle-to-gate emissions, because this is when the most significant reduction in the embodied carbon of concrete can be achieved. The embodied carbon associated with the remaining stages – construction, use and end of life – is likely to be fairly similar for every frame.
The tool also only considers the structural frame itself – it does not consider cladding, finishes, fit-out or services. These can have a significant impact on embodied carbon, and so should not be overlooked when making comparisons. A whole-life carbon assessment is recommended to account for elements beyond, but impacted by, the structural frame, such as foundations, building height and service life, as well as the potential carbon savings from omitting finishes and using thermal mass for passive cooling and heating. Concept Design Tool Version 5 can be downloaded from concretecentre.com/concept
Photo Tim Crocker, Dan Hopkinson, Peter Cook