Recycled concrete paste
Heidelberg materials has developed a process for breaking down old concrete so that it can absorb the carbon emissions from cement production, using A fraction of the energy
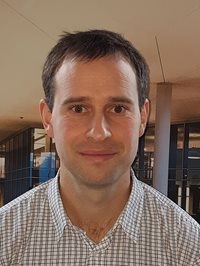
A remarkable new technology being developed by Heidelberg Materials has the potential to greatly enhance the value of recycled concrete, while simultaneously capturing significant amounts of CO2. At a trial in Ribblesdale, Lancashire, the company used 15 tonnes of recycled concrete paste (RCP) to capture 1.5 tonnes of CO2 in just 20 minutes.
The project is led by R&D programme manager Dr Jan Skocek. “Although this technology can only capture around 10% of flue-gas CO2, it is cheap and efficient, so can become a useful part of any carbon capture system,” he says. “Better still, the RCP that has been through this process is a highly reactive material that can be used to make new concrete. It’s like fly ash on steroids.”
The process begins with a new mechanical technology that can “unmake” concrete, partly restoring it to its constituent parts of sand, cement and aggregate. “Usually, when concrete is recycled, it is almost always simply crushed,” Skocek says. “Some is used as filler in new concrete, but the majority becomes rubble and has a low-value future as road base or backfill.
We have developed a new process, selective separation, which uses rubbing and shearing motions to separate old concrete.” The result is RCP – a fine powder comprising 60% cement and 40% very fine sand and aggregate. The remaining larger particles of sand and aggregate can simply be reused as if they were new material, says Skocek. For the RCP, there are three options.
“The easiest is to use it as a filler, adding it to cement in the same way limestone is sometimes used. It is not reactive, so 15% is about the highest proportion. Or you can use it to replace some limestone in the production of clinker. This saves raw material and some carbon emissions. But the most exciting way is to get it to absorb CO2 – a process that mineralises the CO2, storing it forever within the chemical structure of the RCP.”
At Heidelberg Materials’ Hanson plant in Ribblesdale, the RCP powder was mixed with water to form a slurry, then sprayed into the scrubber that cleans exhaust gases from cement production. “Normally the scrubber absorbs mainly sulphur oxides to prevent atmospheric pollution – it is not designed to capture CO2. But the RCP slurry captures both, absorbing CO2 quickly, and in the process becoming a new and, we think, very useful material.”
When the RCP binds with CO2 it becomes carbonated, while other elements in the mix form a new phase known as alumina silica gel. “It is then a highly reactive material that can be used as a cement substitute, and one that can be used to create very strong concrete with rapid strength gain – much faster than fly ash, for example.”
To take the technology forward, Heidelberg Materials’ will this year commission its first full-scale selective separation plant in Poland – able to process 150 tonnes of old concrete per hour. Next year, RCP from this plant will be used in a new, specially designed cement-works scrubber, also in Poland.
This pilot plant will continually mineralise around 100kg of CO2 per hour, and because it is a mechanical process, requiring little heat, it uses about a tenth of the energy of traditional carbon capture. “The pilot will enable us to finetune the process and learn how best to scale it up,” says Skocek. “At the same time we will continue our research into the properties of carbonated RCP and how to maximise its potential.”
He has been involved in various stages of developing RCP since joining the company as a scientist in 2012: “But now I am also handling business development. It is time to make this science work in the market.”
Photos Chris Underwood
Interview by Tony Whitehead
Published in CQ Spring 2023