Robotic formwork
“You waste less and significantly reduce the carbon involved in construction” “Rather we are about moving from mass production to mass customisation – making it easier to design and build efficiently.”
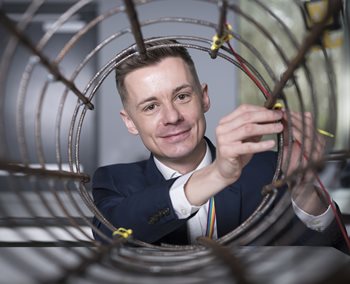
You may have seen those pin-mould toys that make popular stocking-fillers; press your hand onto the bed of closely-packed blunt metal pins and – hey presto! – a 3-D sculpture of your hand. The Amazon listing promises that the “possibilities are endless” and invites buyers to “let their imagination run wild”.
Doing just that is the ACORN team – a group of researchers at Cambridge, Dundee and Bath universities. Digital design experts at Bath are creating software tools that will be used – among other things – to power a giant 8m x 4m pin-mould in Cambridge to become bespoke formwork at the touch of a return key.
Heading up ACORN in Cambridge is Dr John Orr, lecturer in concrete structures: “Pin-moulds have already been used to make precast facade panels, but we are looking to build on the idea – for example, by having robotic arms place reinforcement within the flexible moulds and using them to make more efficiently designed structural elements.”
The smarter production of columns and beams – elements that use just enough material and space to perform their structural function and no more – is the primary aim of ACORN. “The key benefit, compared with standard planar formwork, is that you waste less and so significantly reduce the carbon involved in construction,” explains Orr. “But our approach also involves taking more manufacture off-site and realising other benefits such as faster construction and safer working.”
Optimising structures in this way – entering a world of tapering columns and “fish-belly” beams that are thicker in the middle where the strength is needed – has been discussed before. But contractors and engineers are usually sceptical and fear higher design costs and questionable buildability. They should be reassured by Orr’s approach: “I did my first degree at Bath University partly because it had a combined department of architecture and civil engineering. I think having an architect doing a squiggle and then passing it on to an engineer to build is not a good way of doing things.”
Addressing the disconnects between design and practicality is at the heart of the ACORN project: “We do the messy concrete stuff here in Cambridge, but the digital side, mainly being done at Bath, seeks to optimise structural design and ensure it links coherently to automated or robotic manufacturing, while at the same time developing computational tools for constructability.”
ACORN is not about creating impossible designs, says Orr: “Rather we are about moving from mass production to mass customisation – making it easier to design and build efficiently.”
Staying true to his roots then, Orr wants ACORN to use the latest tech to allow architecture and engineering to work as one from the start. If they get it right, buildings will need less material and enjoy smaller carbon footprints. And some of them, at least, will look like nothing we have seen before.
Words by Tony Whitehead
Photo Paul Burroughs
Published in CQ Spring 2020